By Chuck Olson
Those collision businesses that develop an effective diagnostic scan process will see the benefits almost immediately.
A diagnostic process—like strategy-based diagnostics—performed by a qualified diagnostic specialist can save a collision repair facility money, cut back touch-times, improve capacity, reduce the risk of legal liability, and, most importantly, improve the safety of motorists on the road.
It can even improve client and insurer relations.
When maintenance items—such as failing batteries—and worn components, switches and electrical motors are identified during diagnostic inspections, an effective diagnostic scan process will allow a repair business to determine who is responsible for the cost of the repair—be it the vehicle owner, auto insurer or manufacturer— rather than just being added to a loss claim.
Presenting all parties with the necessary, accurate test and inspection results is sure to win trust. While customers might not be happy to have to pay for a battery, addressing maintenance opportunities becomes easier when the problem is readily identified and documented.
Properly trained and experienced diagnostic technicians are able to zone-in on the true needs of a repair, reducing unnecessary procedures and identify those commonly missed safety items early in the repair process.
They are also able to better determine what procedures an insurer is or is not responsible for related to a loss claim—and to document the evidence.
At the very least, presenting all parties with the necessary, accurate test and inspection results is sure to win trust.
On the other hand, those collision businesses that do not have an effective diagnostic scan process may expose themselves to legal dangers—and their customers to physical ones.
Collision facilities may not even realize what is wrong with their diagnostic approach. Unfortunately, there are some serious misconceptions within the industry about how to use scan tools and what exactly there capabilities are.
The most significant of these misconceptions is that by pulling diagnostic trouble codes (DTCs), a scan will tell you exactly what needs to be done to fix a vehicle. Unfortunately, a basic code-pull barely scratches the surface of what is involved in the scanning and diagnostic process.
It is pretty simple to clear DTC codes and to get a report saying they are all clear. Many drivers and collision business owners believe that ‘all clear’ really means ‘all clear.’ This isn’t—at all—the case. If that sounds like the approach your business is taking, you are not in the clear—, especially from a liability standpoint.
In reality, by executing clear code functions, the automotive computer system receives a reset command from the scan tool.
The module’s immediate memory of sensor and fault information is wiped—which usually causes the system to forget the out-of-range sensor data that set them off in the first place! Any experienced automotive technician will agree retrieving and/or clearing trouble codes is only the starting point.
Effective diagnostics involves using all the functions and data available with modern scan tools.
At Airpro Diagnostics we use several test and data fields we call “component level scanning”. To make effective use of the information, a trained technician has to go into the individual modules and check through the code’s status and data within each.
But even this does not always give you the remedy. By pulling information from the relevant module, the technician will see between 30 and 100 lines of data. This will give them enough information to significantly reduce the shortlist of possible causes.
Further investigation will allow them to narrow things down even more. Here’s the caveat, though. The numbers reflect data—data which may or may not reflect reality—and when it comes to verifying the situation in the vehicle, a remote diagnostic technician needs a capable auto repairer at the vehicle to investigate. In order to meet the criteria to say the system is good, it has to pass a physical-check, which may or may not reveal that the problem is still there.
Take, for example, the diagnostic specialist discovers that a DTC or data is reporting a lean condition. On the basis of the DTC, the cause could be related to the voltage feed, the command fuel delivery system, or any number of other causes— including a problem with the sensor itself that requires further inspection. And don’t forget about the required calibrations, programming and initialization needed after repairs.
Another common misconception relates to how scans should be performed—and who should be performing them. It is widely—and incorrectly—believed that a single automotive technician can be responsible for the entirety of the scanning and diagnostic process, on every vehicle while using a single scan tool.
As someone who has worked in vehicle diagnostics for over 30 years, the idea that any single technician would have the knowledge required to be effective on every vehicle seems ridiculous. Leaving the speed at which the technology is changing aside, knowing how to accurately interpret the diagnostic information for one brand of vehicle won’t prepare you for another one.
In fact, at AirPro, my colleagues—who have often spent years working in diagnostics at the dealership level prior to joining the team— spent two full months mastering a single OEM diagnostic language. While they will then go on to become familiar with the diagnostic language of two other brands, most will only ever be a top tier specialist with one or two brands.
Of course, the notion of mastering every OEM diagnostic language isn’t half as terrifying to us remote diagnostic technicians as the notion of being responsible for performing the physical inspection of the vehicles that we scan.
Developing a diagnostic scan process isn’t easy. If it was, our company, AirPro Diagnostics, which provides repair facilities with access to diagnostic experts, wouldn’t exist.
If you wish to develop one, though, it might be best to keep this analogy—between vehicle diagnostics and the medical field in mind:
While an MRI or X-Ray technician operates the machine, it is the radiologist who interprets the results and provides a surgeon with the information needed to conduct the surgery.
In the case of a vehicular scan, A technician with basic skills can connect the tool.
It is the diagnostic technician who should be interpreting the results and the repair technician who is performing the surgery.
Yes—you read that right—just retrieving and clearing trouble codes is a bit like handing a scalpel to an X-ray technician!
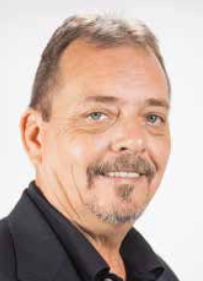
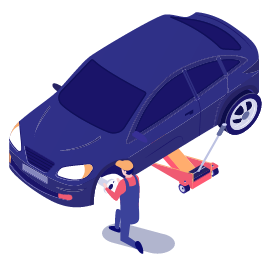
The co-inventor of the first remote vehicle programming system and method, diagnostics expert Chuck Olsen is one of the founders of AirPro Diagnostics, where he now serves as its senior vice president of automotive technology solutions.